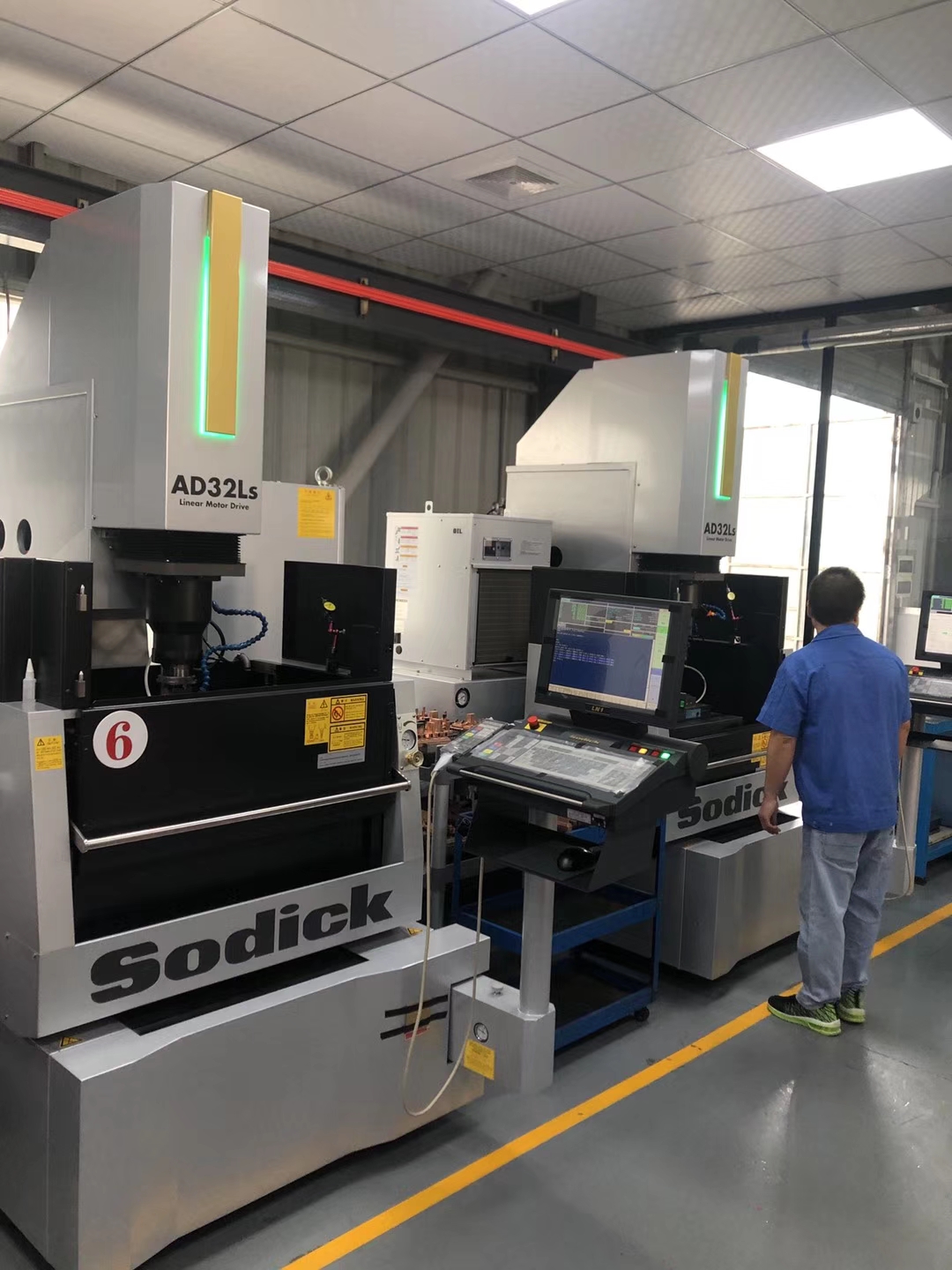
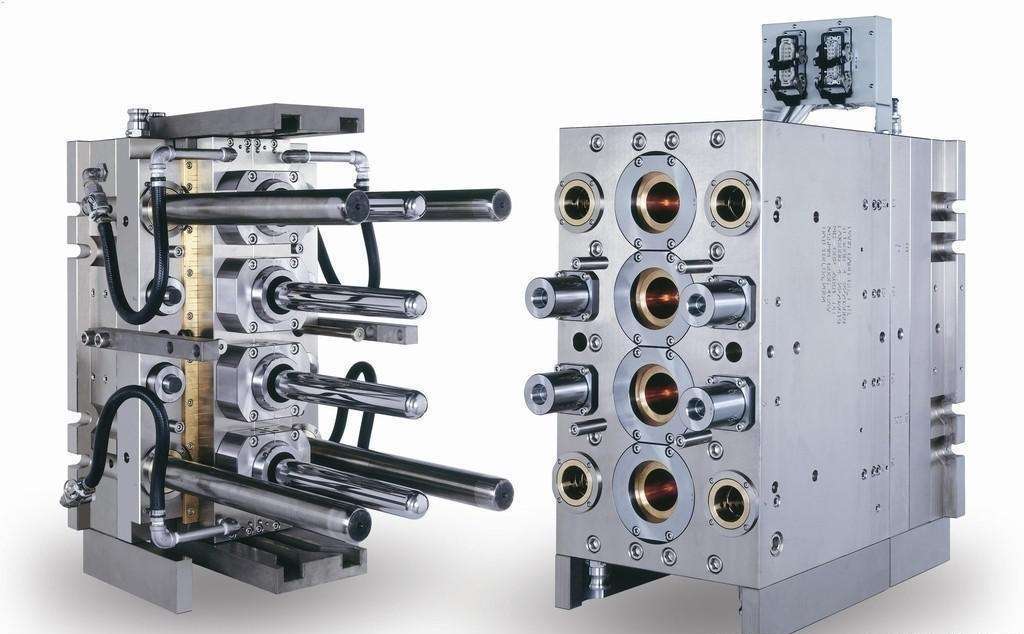
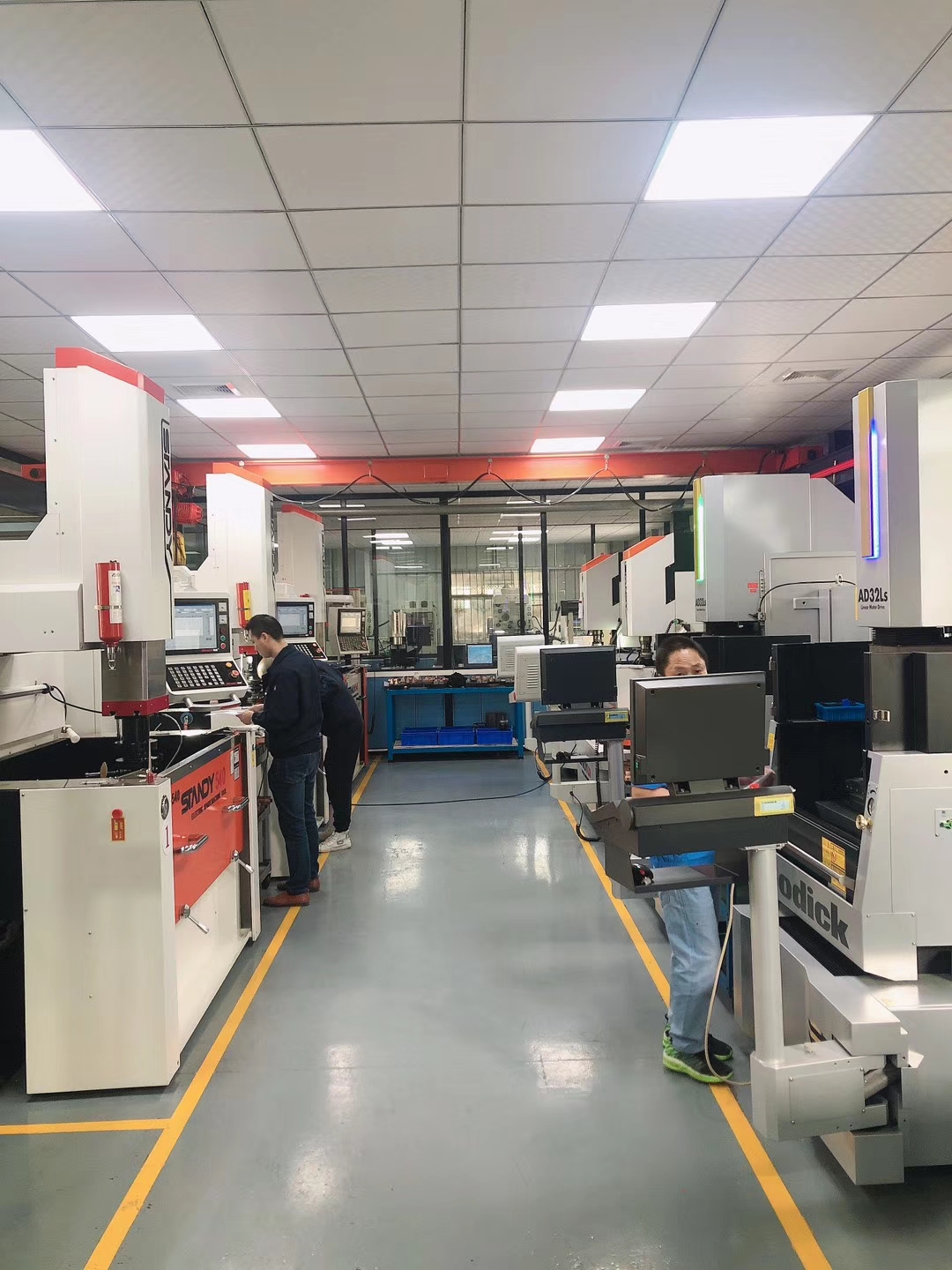
As injection mold tooling manufacturer, we are committed to providing high quality injection molds for global customers.
We adopt special excel steel material from famous steel companies, such as:schmolz-bickenbach, Assab, SorelForge,LKM. All standard components
in the plastic injection mold tooling are adopted DME, HASCO, Progressive, PCS, Parker standard or as custom's request. The most of our injection molds are exported to Canada, USA and Europe.
Our injection mold tooling can product automaticcaly in our customers side
Our team completes projects on time and right the first time for more 20 years. We have a 95% on time delivery with our customers. 99% of our injection molds are good on at the first shot.
Our experienced operators and a variety of large and small machines enable us to handle complex shapes and close tolerances.
The max.mold dimension is 1800x1000mm, max.mold weight is 10 tons.
Our engineers design the full 3D mold tooling with UG-NX software according to the our mold standard or customers request.
We will send the mold design to our customers, and work with customers to find the best solutions for their unique needs.
After getting the approval to cut, then we start to manufacture the injection mold toolings. If the customers have an ECN that needs to be done,
We are very flexible to work with, and will turn it around quickly.
We continually expand our capabilities to meet each challenge and use the latest
machines in High speed manufacturing for Quick turn around and excellent Quality.
With the modern industrial's development, the plastic products industry are widely used in agriculture, daily life, and other fields;
quality requirements have become more sophisticated,the production cycle became increasingly short. The quality of tooling design, advanced
manufacturing equipments, reasonable processing and quality materials and components are important conditions for injection molding quality forming.
So we strive quality and devote extensive resources to ongoing employee training, and pay attention to line disruption prevention and component failure reduction.
Our highly skilled and competent toolmakers can accomplish in the use of the equipment and software necessary to produce even the most intricate injection molding toolings.
They will give you leading edge process and equipment in the hands of skilled and experienced crafts, complex plastic injejction mold tooling are our specialty.
Examples given are the most common types as used by Viewmold. The Customer will specify the general steel types. HRS – Hot rolled steel –SAE 1030: Ejector housing plates, clamping plates, back-up plates, support pillars, mold “feet” (NOTE: Due to the limited availability of HRS, all mold plates can be 4130/4140 (#2) steel.)
4130/4140 (#2 Steel) - Prehardened 30-36 RcC : General mold base plates
P-20 – Prehardened 30-36 RcC : High grade base plates, large cores and cavities, core and cavity inserts, slides, sub-inserts
420M (Prehardened 420 stainless steel) - Prehardened 30-35 HRC : large cores, cavities, inserts, slides
S-7 - Air hardening 54-56 RcC – Cavities, Cores, inserts, lifters, stripper rings, slides
420 SS - Stainless 50-52 RcC – Cavities, cores, slides, inserts
FP-100 Lamina Bronze – Wear plates – Must provide grease grooves. O-1 - Oil hardening 58-62 RcC – Gibs, slide guides, wear plates Ampco-18 – Gibs, slide guides, and wear plates
*All mold plates are minimum of SAE 1030 steel.
*Core and Cavity blocks (In-solid designs), Core and cavity inserts, sub-inserts, and other non-moveable items are to be constructed with a minimum of P-20 steel.
*All ejector pins, screws, locating ring, waterline components adopt DME or HASCO standard.
*Slides, lifters, bar ejectors, and similar actions can be constructed of P-20 steel also, but must have a minimum of 3-degrees shut-off on all seal surfaces. Nitriding is required otherwise, as in the case of straight wall lifter designs. Hardened S-7 steel should be considered for all lifter designs.
*Slides must have bronze wear plates with grease grooves.
*Ejector plates must be guided with at least two guide pins and ejector guide bushings minimum. The amount will be determined based on the mold size and number of ejector plate activated actions.
*Integral parting line locks must have bronze wear plates if the interlock angle is less than 10-degrees. Standard inserted hardened interlocks are acceptable as the part design permits. All interlock designs must protect internal shut-offs.
*Cooling is required in all part-related features insofar as possible, and in mold plates as required for specific temperature control, such as in plates encompassing hot runners, valve gate actuators, etc.
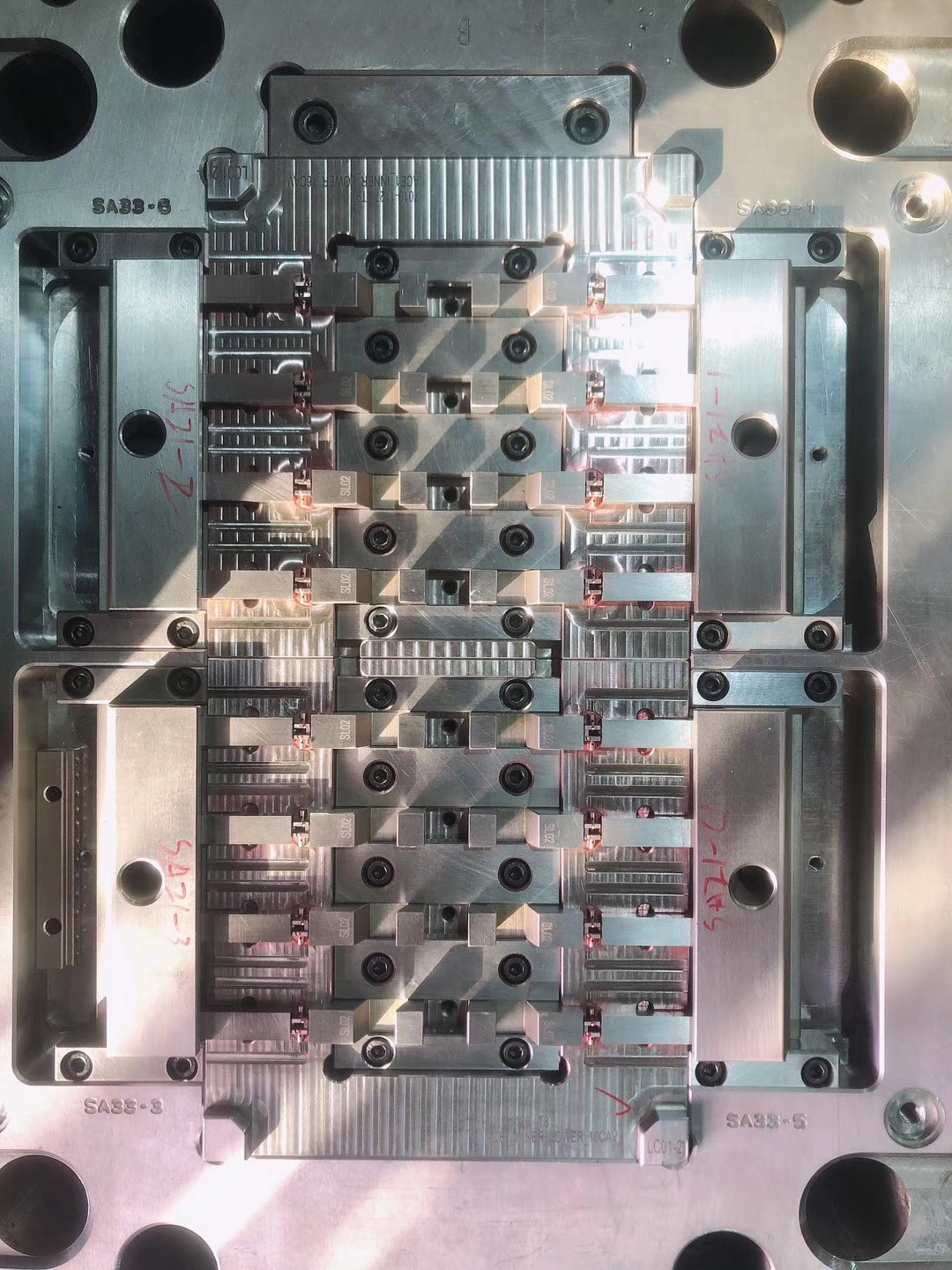
*All mold plates are minimum of P20 steel or stainless steel.
*Core and Cavity blocks (In-solid designs), Core and cavity inserts, sub-inserts, and other non-moveable items are to be constructed with a minimum of H13 steel.
*All standard components adopt DME HASCO standard, all standard components can be interchange easily.
*Slides, lifters, bar ejectors, and similar actions can be constructed of H13 steel also, but must have a minimum of 3-degrees shut-off on all seal surfaces. Nitriding is required otherwise, as in the case of straight wall lifter designs. Hardened S-7 steel should be considered for all lifter designs.
*Slides must have bronze wear plates with grease grooves.
*Ejector plates must be guided with at least four guide pins and ejector guide bushings minimum. The amount will be determined based on the mold size and number of ejector plate activated actions.
*Integral parting line locks must have bronze wear plates if the interlock angle is less than 10-degrees. Standard inserted hardened interlocks are acceptable as the part design permits. All interlock designs must protect internal shut-offs.
*Cooling is required in all part-related features insofar as possible, and in mold plates as required for specific temperature control, such as in plates encompassing hot runners, valve gate actuators, etc.
1: Part check, all size are OK or acceptable, Parts have no injection molding defects.
2: The injection mold tooling running, the tooling can smoothly run without any issues.
3: automatic running: The tooling will run 1000 shots automatecally, we'll send video of automatic running mold tooling to our customer.
4: appearance check.
5: Ejection, Return system check.
6: cooling system check.
ht 7: Cold Runner check
8: Hot Runner System
9: lifter and slide check
10: hardness check for core, cavity, inserts, lifter and slides. 11: assembly check. 12: Packing check.
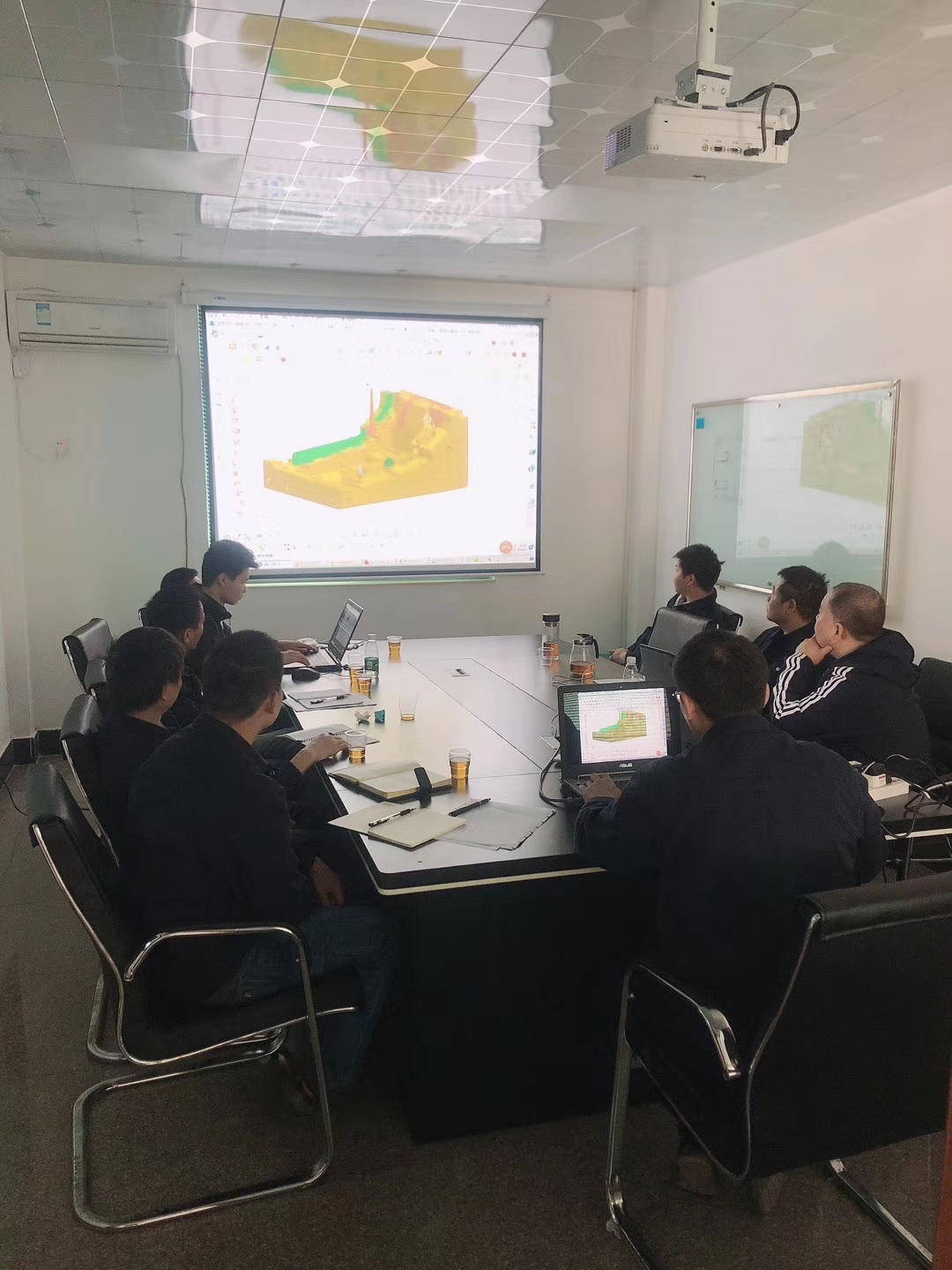
The life of injection mold tooling is at 300,000 or 1,000,000 if the hardness of steel is more than HRC48.
Our injection molds can very smoothly run automatically without any issue within the life.
All components of mold base will adopt DME's or HASCO's standard.
You can retain 10%-20% final payment of tooling until our injection molds runs in your side for 1 month.
If you have any plastic injection molds projects,please contact us with Email:sales@viewmold.com or request a quote online..
As a excel injection mold tooling manufacturer, we guarantee that you will get a quick feedback. Our responsive specialists have highly experienced in the areas of plastic injection molding and toolings, from design tips to material selection and control for the costs.
Our company also provides metal manufacturing and plastic extrusion services for global customers.
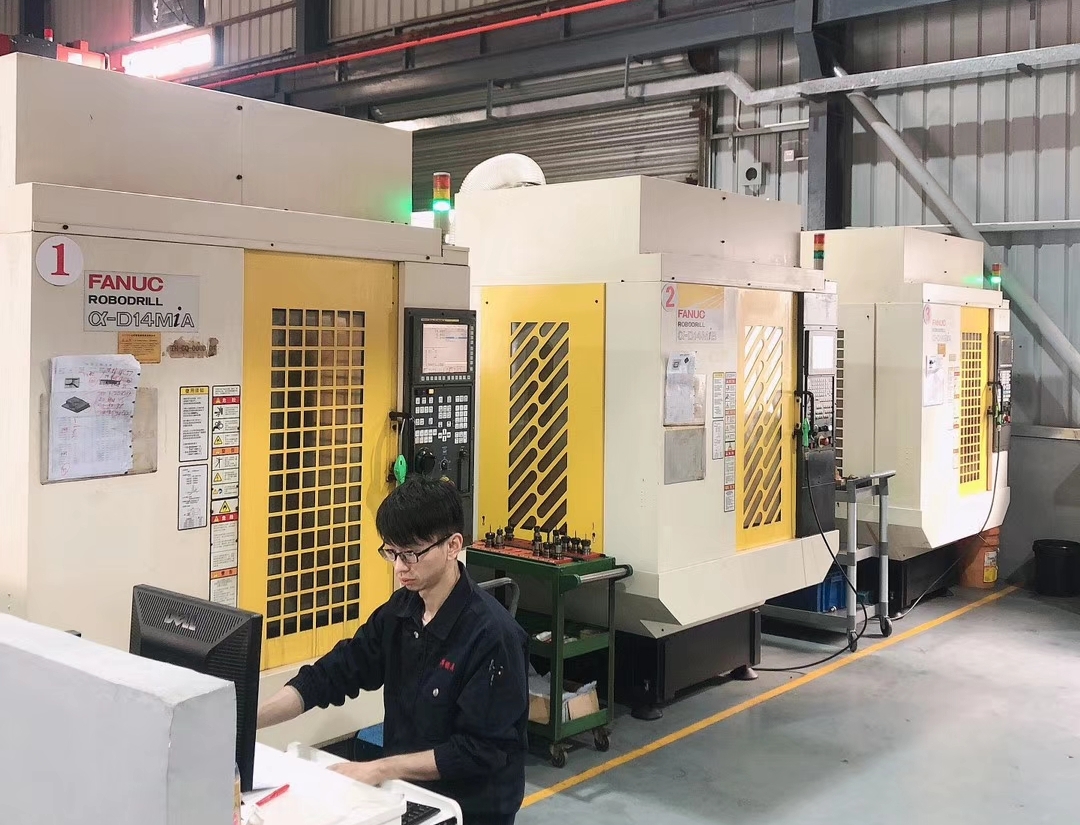
high precision
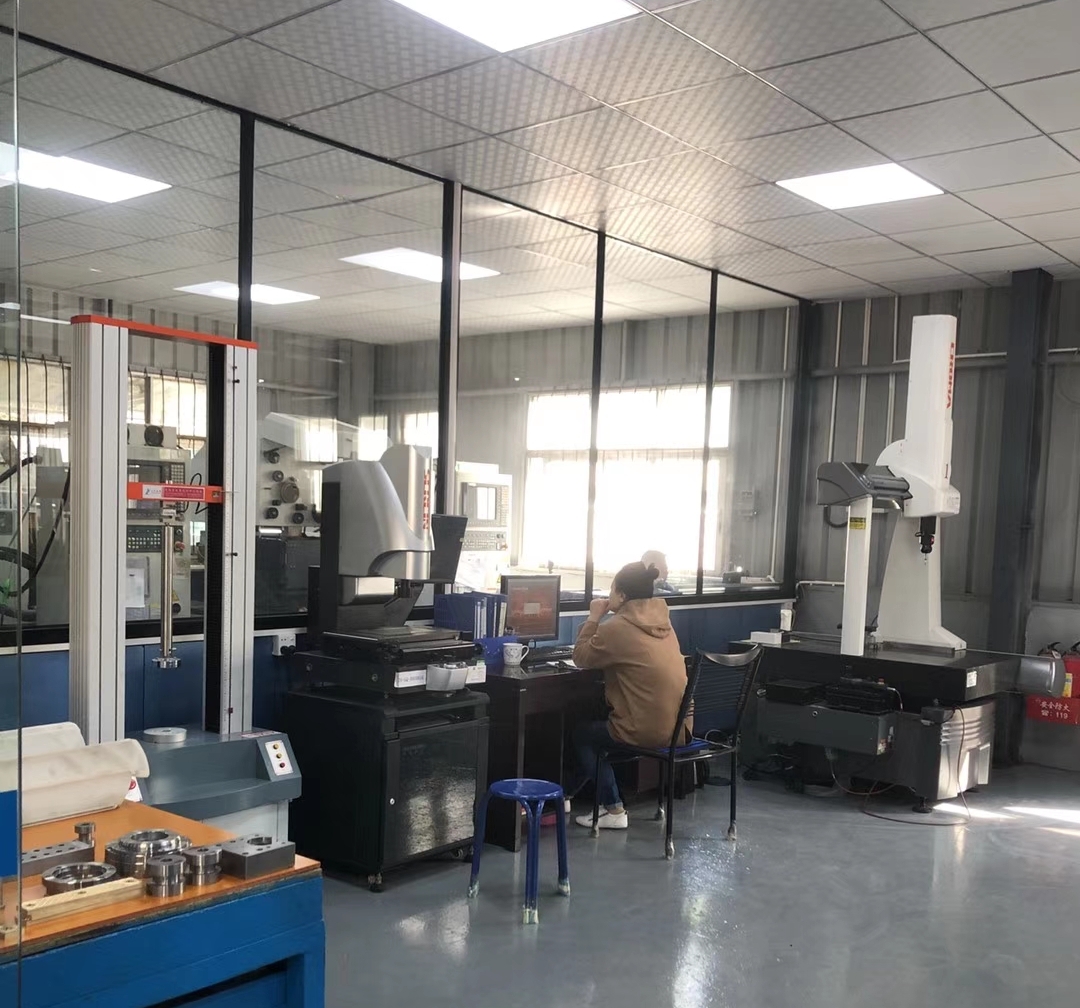
inspection room
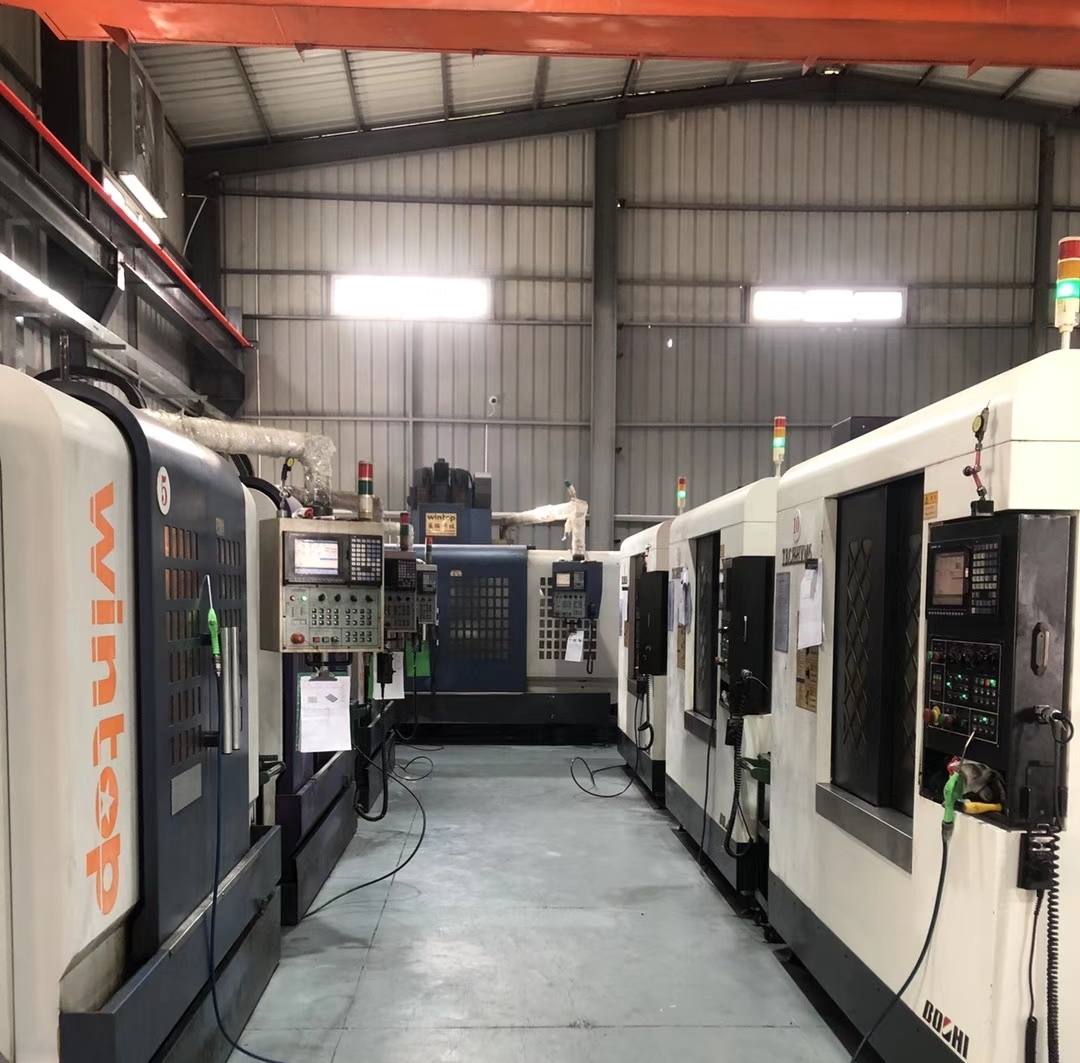
CNC_manufacturing
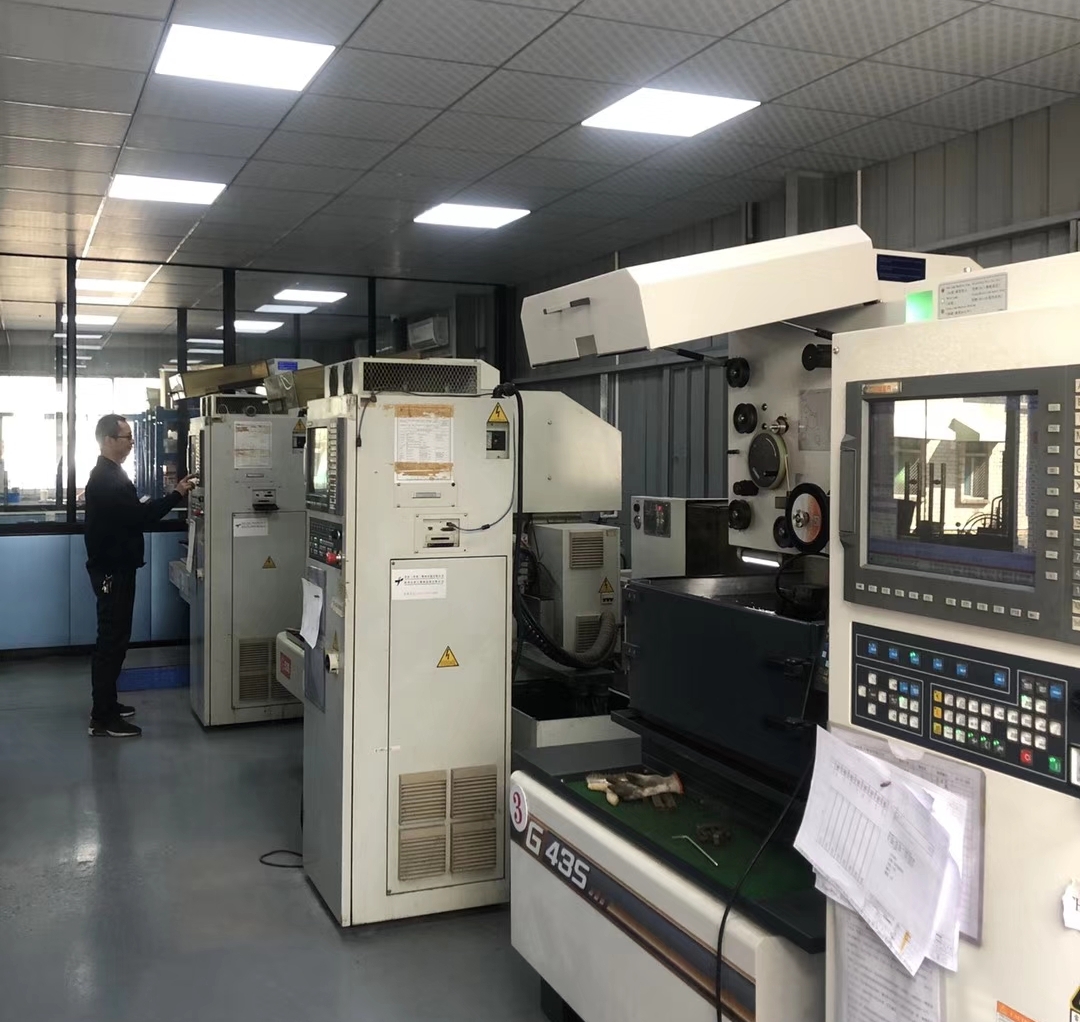
precise slow wire cut.
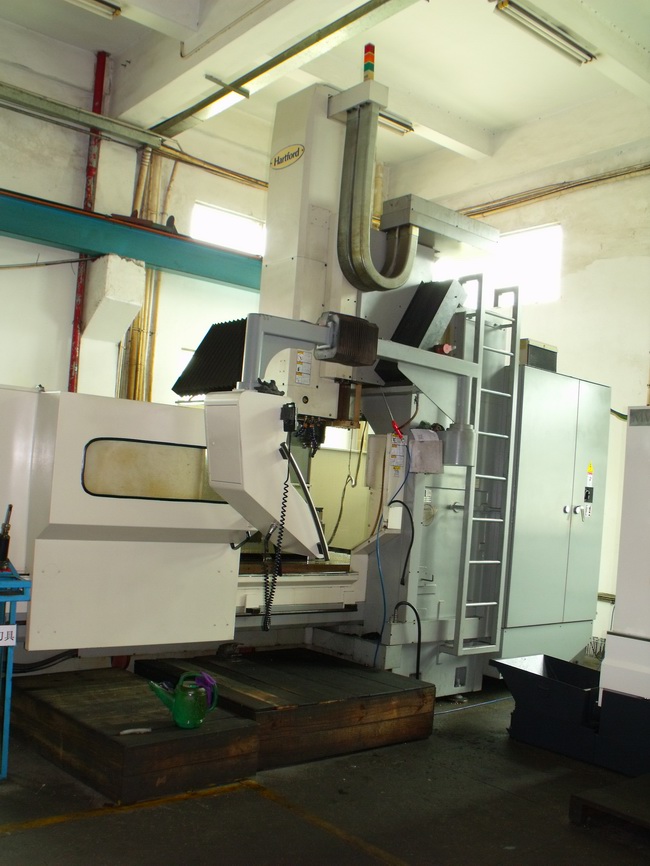
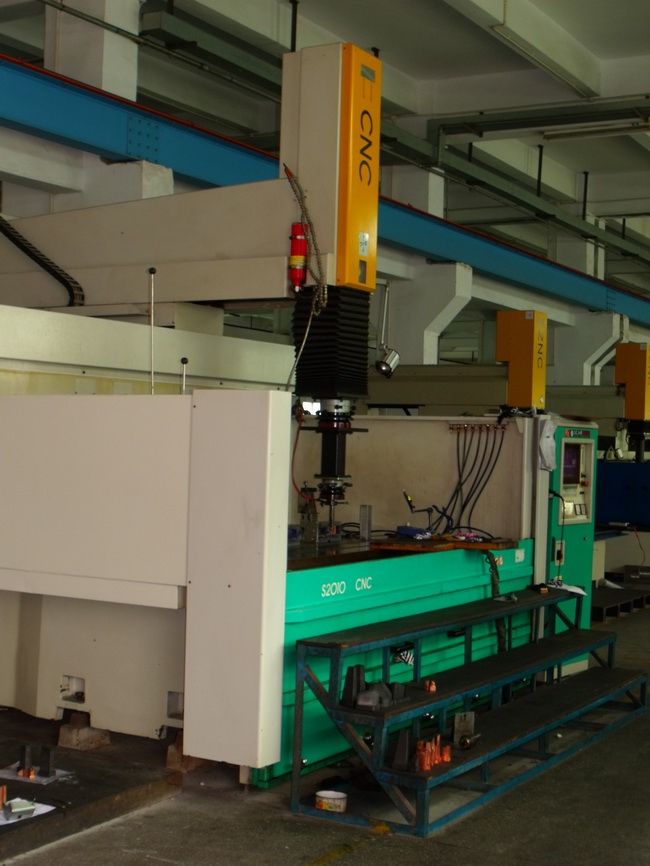
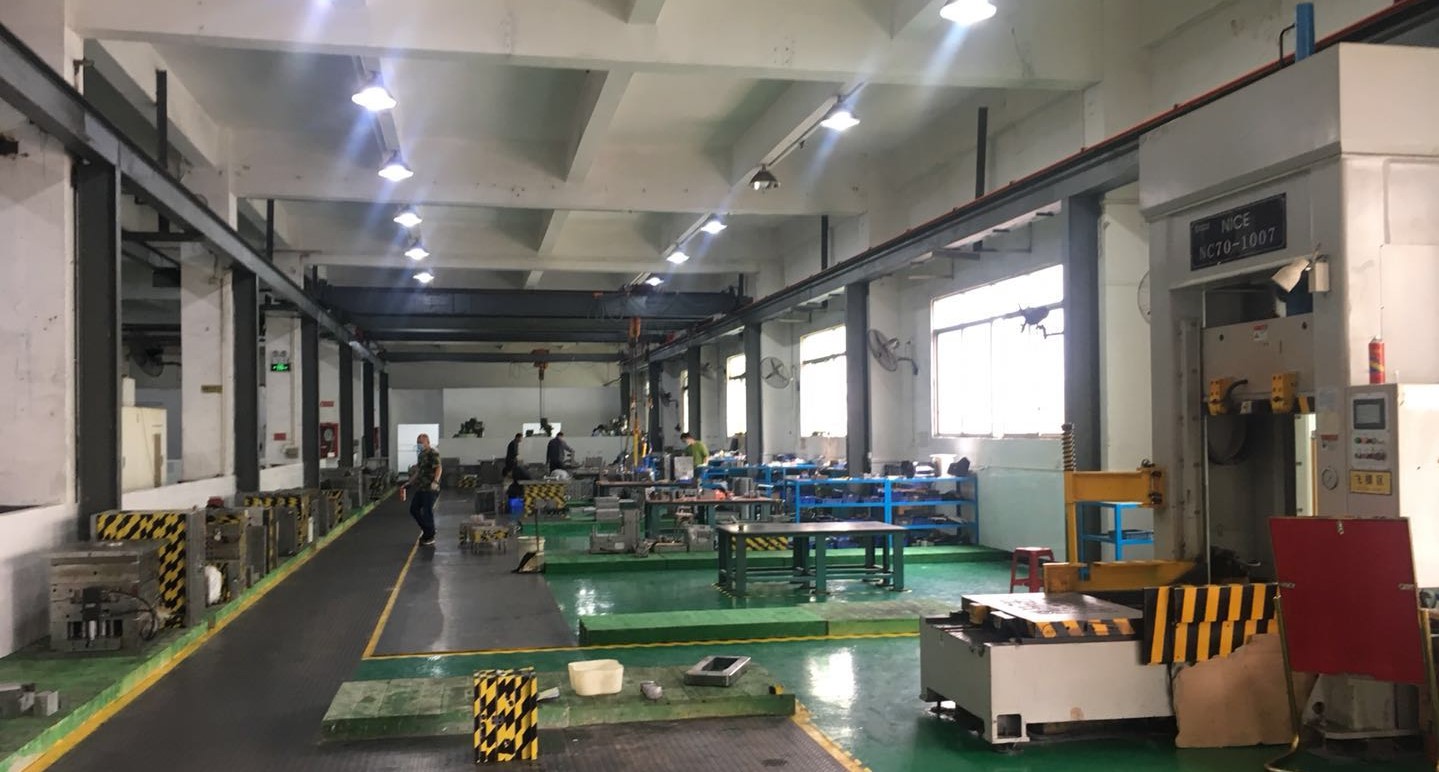
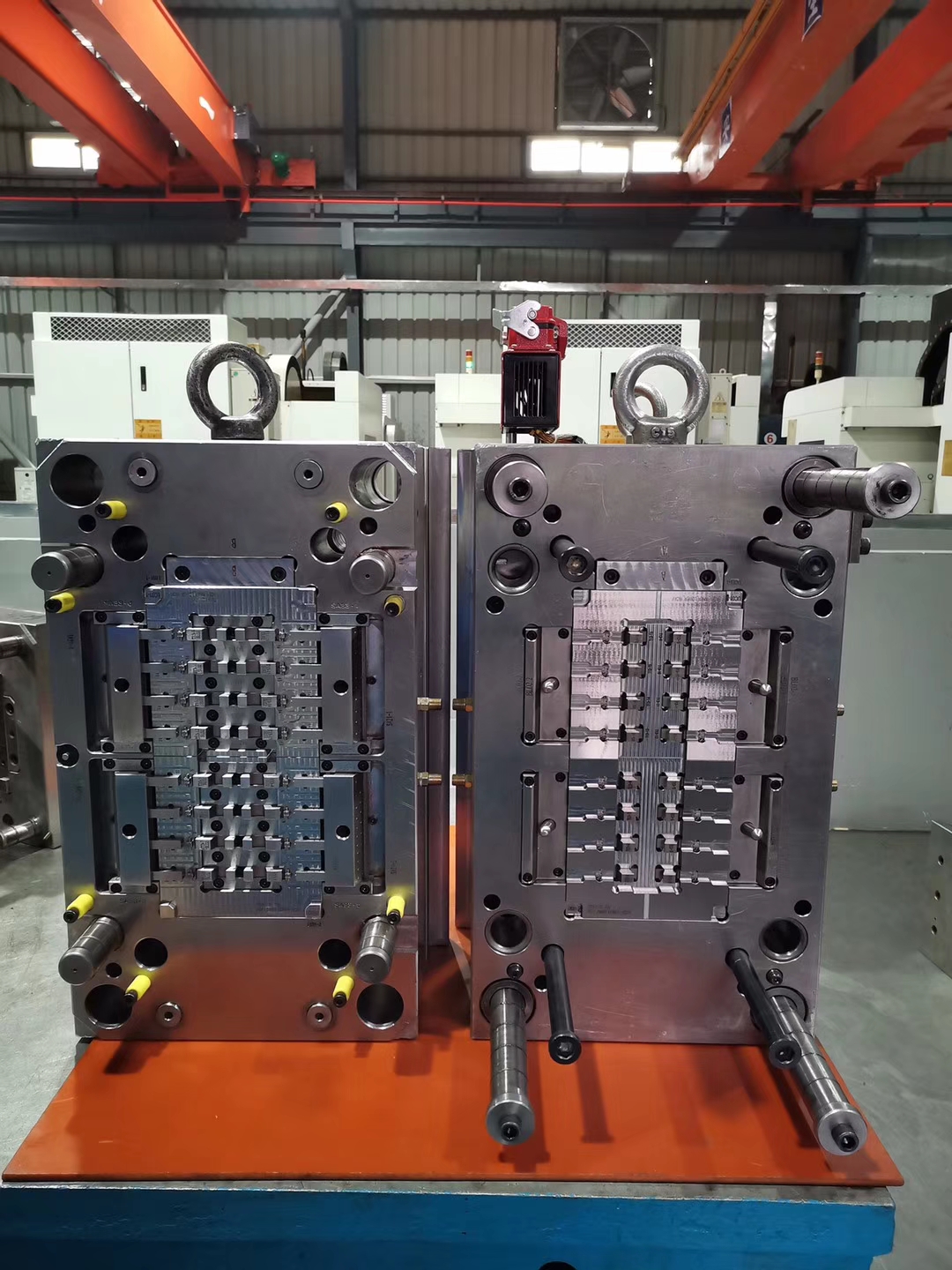